High-temperature alloys, also known as hot-strength alloys, super alloys, refers to a class of metal materials that can work for a long time in high-temperature environments and under certain stresses, with good resistance to high-temperature oxidation and thermal corrosion, as well as excellent high-temperature strength, fatigue strength, creep fracture toughness and other comprehensive properties. These alloys are mainly used in the aerospace field, energy field and ship's turbine engine.
I. Classification of high temperature alloys
1, according to the matrix organization materials can be divided into three categories: iron-based, nickel-based and cobalt-based.
(1) iron-based high-temperature alloys, also known as heat-resistant alloy steel, heat-resistant alloy steel can be divided into martensitic, austenitic, pearlite, ferritic heat-resistant steel and so on according to its normalization requirements. Iron-based high-temperature alloys use a lower temperature (600 ~ 850 ℃), but its medium-temperature mechanical properties are good, and similar nickel-based alloys are comparable or better, coupled with cheaper, hot work deformation is easy to generally used in the engine in the working temperature of the parts, such as turbine disks, magazines and shafts and other parts.
(2) Nickel-based high-temperature alloys use the highest temperature (about 1000 ℃), widely used in the manufacture of aviation jet engines, a variety of industrial gas turbines, the hottest end of the parts, such as the turbine part of the working blades, guide vanes, turbines and so on.
(3) Cobalt-based high-temperature alloys have good castability and weldability, can be used at high temperatures of 700 ~ 1050 ℃. It takes cobalt as the main component, and its typical representative is K610, containing more than 58% cobalt. Due to the expensive price of cobalt, resource shortage, so domestic and foreign rarely used, the existing grades are K640, K644, GH188 and so on.
2, according to the preparation process can be divided into deformation of high-temperature alloys, casting high-temperature alloys and powder high-temperature alloys.
(1) deformation of high-temperature alloys
Deformation of high-temperature alloys refers to the ingot cold, hot processing into a variety of profiles or parts blanks, and finally made of hot parts of the high-temperature alloys, the key is the alloy ingot has the ability to form. Compared with the casting high temperature alloy, deformation of high temperature alloy alloy alloy alloying degree is low, therefore, the melting point is higher, the upper limit of the hot working temperature is higher, the alloy recrystallization temperature is lower, reduce the lower limit of the hot working temperature, therefore, the deformation of the high temperature alloy hot working range of the casting of high temperature alloy wide. According to the different elements of the matrix, deformation of high-temperature alloys can be divided into iron-based deformation of high-temperature alloys, nickel-based deformation of high-temperature alloys and cobalt-based deformation of high-temperature alloys.
(2) cast high-temperature alloys
Cast high-temperature alloy is remelted by the alloy ingot directly after pouring or directional solidification into parts of high-temperature alloys, its development began in the 1940s. Cast high-temperature alloy no longer consider forging deformation performance, can be cast by precision casting method or directional solidification process casting out the shape of complex and have a smooth inner cavity of the hollow thin-walled blades without margins. Therefore, the casting of high-temperature alloys, the total number of elements to be significantly higher than the deformation of high-temperature alloys, in which the solid solution strengthening elements added elements such as Re, Ru, refractory metal elements to increase the content of W (some alloys more than 10%) precipitation strengthening of alloying elements, in addition to Al, Ti, but also to add Nb, Ta, Hf, V and other elements.
Casting high-temperature alloys according to the solidification method can be divided into isometric crystal casting high-temperature alloys, directional solidification column crystal high-temperature alloys and single-crystal high-temperature alloys three categories. One of the single crystal high temperature alloy as a new type of high temperature alloy, is the use of directional solidification process to eliminate all the grain boundaries formed by the high temperature alloy, the metal is made up of a single crystal, so it is called single crystal high temperature alloy. The grain boundary is a variety of distortions within the metal, defects and impurities gathered in the zone, the grain boundary at room temperature strength is higher than the inside of the crystal, but at high temperatures are prone to slip, when the intensity of the grain boundary at high temperatures lower than the inside of the crystal, the strength of the metal will decline. Therefore, the use of directional solidification technology to eliminate grain boundaries, the single crystal high temperature alloy obtained excellent performance. At present, almost all advanced engines have been used in single crystal alloy turbine blades or guide vanes.
(3) powder high temperature alloys
With the heat-resistant alloy working temperature is getting higher and higher, the strengthening elements in the alloy is more and more, the more complex the composition, resulting in some alloys can only be used in the cast state, can not be hot working deformation. And the increase in alloying elements so that nickel-based alloys solidified composition segregation is also serious, resulting in uneven organization and performance. The use of powder metallurgy process to produce high temperature alloys can solve the above problems. Because the powder particles are small, powder cooling speed, eliminating segregation, improve the hot workability, the original can only casting alloy into hot workable high-temperature alloys, yield strength and fatigue properties are improved, powder high-temperature alloys for the production of higher strength alloys have produced a new way. Powdered high-temperature alloys are mainly used in the manufacture of high-thrust ratio advanced aero-engine turbine disk, also used in the production of advanced aero-engine compressor disk, turbine shaft and turbine baffle and other high-temperature hot-end parts.
3, according to the strengthening mode is divided into solid solution strengthening, precipitation strengthening, oxide dispersion strengthening.
(1) solid solution strengthening
The so-called solid solution strengthened that add some alloying elements to iron, nickel or cobalt-based high-temperature alloys, the formation of a single-phase austenitic organization, solute atoms to make the solid solution matrix matrix distortion, so that the solid solution in the resistance to slip increased and strengthened. Some solute atoms can reduce the lamination energy of the alloy system, improve the tendency of dislocation decomposition, resulting in cross-slip difficult to carry out, the alloy is strengthened, to achieve the purpose of high temperature alloy strengthening.
(2) Aging precipitation strengthening
The so-called aging precipitation strengthening that alloy workpiece by solution treatment, cold plastic deformation, placed at a higher temperature or room temperature to maintain its properties of a heat treatment process. For example: GH4169 alloy, the highest yield strength of 1000MPa at 650 ℃, the production of blade alloy temperature up to 950 ℃.
(3) diffusion strengthened
Diffusion strengthened high temperature alloys with high high temperature strength and low stress coefficient, widely used in gas turbines heat-resistant oxidation parts, advanced aviation engines,.....
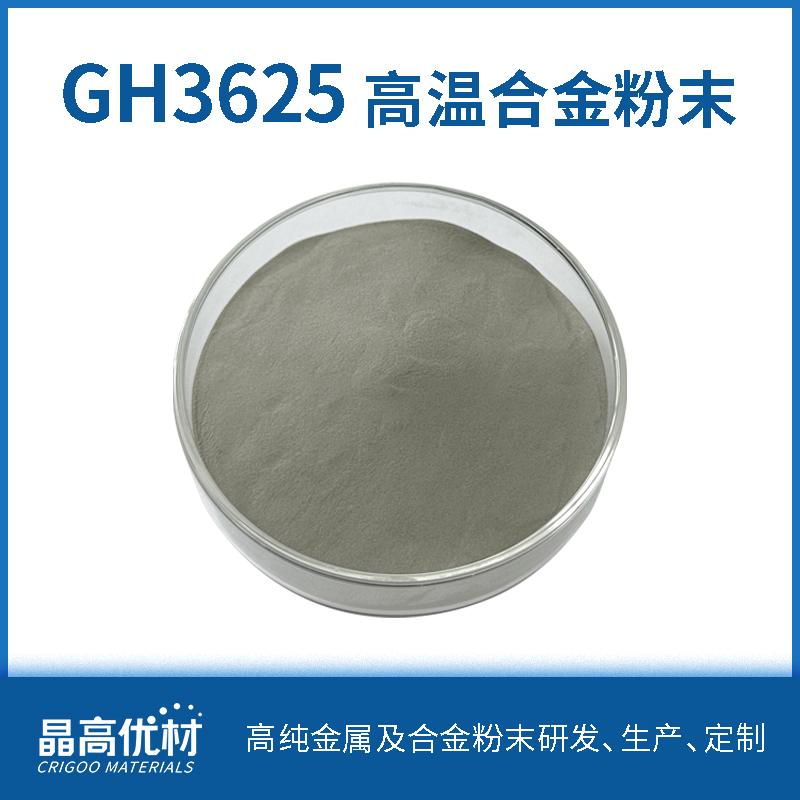