With the increasing flight speed of hypersonic vehicles, the demand for lightweight, high-strength and high-temperature resistant alloy materials in the aerospace field is becoming more and more urgent. Currently available materials include high-temperature titanium alloys such as TA15 or Ti65, nickel-based high-temperature alloys, TiAl and Ti3Al intermetallic compounds, etc. Ti2AlNb alloy is a newly developed lightweight, high-temperature-resistant structural material in the Ti3Al series of intermetallic compounds, and it can be used for a long period of time at 650-750°C, and for a short period of time at more than 1000°C. Its operating temperature is more than 100°C higher than that of Ti65, and its density is higher than that of the other alloys. Its use temperature is higher than Ti65 and other high-temperature titanium alloys more than 100 ℃, the density is much lower than high-temperature alloys, its room temperature plasticity, high-temperature specific strength, fracture toughness, creep resistance and other comprehensive mechanical properties are far superior to TiAl and Ti3Al alloys.
Ti2AlNb alloys are often referred to as orthorhombic (O) phase alloys and were discovered by Banerjee et al. in 1988 that this O phase has more slip systems and therefore better ductility. In addition, the O-phase exhibits better mechanical properties such as high strength-to-weight ratio, fracture toughness, oxidation resistance, and formability, and the heat treatment of this alloy produces five main microstructures including fully B2 and α2+B2, lamellar, bimodal-lamellar, equiaxial, and biphasic O-phase microstructures. Its excellent performance has almost become the best choice of high-temperature structural materials for hypersonic vehicles, and has received extensive attention and in-depth research from scholars at home and abroad.
Ti2AlNb alloy related research
01, SLM preparation of Ti2AlNb and its heat treatment of the relationship between organization and mechanical properties
Ti2AlNb intermetallic compounds have good application prospects in the aerospace industry due to their high specific strength and high creep resistance at high temperatures, and selective laser melting (SLM) technology for this material has emerged in recent years. Some experiments were conducted to prepare Ti2AlNb alloys by SLM process, and the characteristics of slat, needle and grain boundary (GB) precipitates after different heat treatments were investigated, and the relationship between the size and volume fraction of precipitates before and after solid solution heat treatment (SHT) temperature and aging treatment (AT) was established. High-temperature tensile tests were conducted on SLM and heat-treated intermetallic compounds, and the relationship between microstructure and mechanical properties was proposed to rationalize the changes in tensile strength and elongation at high temperatures. The experimental results showed that the SLM-treated specimens were dominated by the B2 phase with good room temperature ductility, but the continuous precipitation along the grain boundaries decreased the tensile strength and ductility at 650 °C. After SHT (920 °C) + AT, the maximum elongation (El) at 650 °C was significantly increased due to the precipitation of the large-size slate O + α2 phases. after SHT (1000 °C) + AT, the maximum elongation (El) at 650 °C was significantly increased due to the precipitation of the precipitation of needle-like O phase, the maximum ultimate tensile strength (UTS) of the tensile test at 650°C increased to 820 MPa.
Ti-22Al-25Nb alloys have also been studied synthesized in situ using selective laser melting technique. The data showed that the microhardness of the prepared alloy was 358.1±5.8 HV0.5, and the SLM-produced Ti-22Al-25Nb material annealed consisted of B2 grains, Ti2AlNb and Ti3Al precipitates, with a uniform distribution of elements in the bulk material.
Translated with DeepL.com (free version)
02, Arc additive manufacturing in situ preparation of Ti2AlNb alloy
Arc additive manufacturing technology due to the advantages of high deposition efficiency, low cost, large material utilization and flexible manufacturing of large structural parts, etc., in the ship, aviation, automotive and many other engineering fields has attracted great attention and shows good prospects for application, there is a study on the use of arc additive manufacturing (WAAM) technology in situ preparation of Ti2AlNb alloys, and a systematic study of the composition of the deposition. The results show that the compositional error between the average test value and the design value of the deposits is within 1.1%, but there exists localized segregation in composition and organization. The phenomenon of segregation deteriorated the mechanical properties, with the ultimate tensile properties and elongation averaging 504 ± 38.59 MPa, 0.41 ± 0.03% and 375 ± 32.60 MPa, 0.76 ± 0.05% at room and high temperatures (650 °C), respectively. Meanwhile, the prepared alloys showed a fully layered structure, and the XRD results indicated that the basic constituent phases B2, O and α2 of Ti2AlNb alloys appeared successfully. The in-situ fabrication method demonstrated in this work is expected to significantly contribute to the wide application of AM due to its low cost and high flexibility advantages.
03. Preparation of Ti2AlNb alloy by hot isostatic pressing process
Ti2AlNb alloys have a higher specific strength at elevated temperatures and have been considered as candidates to replace high temperature alloys such as GH4169 in gas turbine engine applications. Despite their high resistance to deformation, Ti2AlNb alloys are typically formed by forging or rolling, and the inhomogeneous microstructure induced by thermomechanical processing of the ingots can lead to large fluctuations in the mechanical properties of Ti2AlNb alloys. Powder metallurgy (PM) offers the potential to address many of the problems associated with the production of large ingots, such as centerline porosity, chemical inhomogeneities, and genetic phenomena of thermomechanically processed organizations.
By optimizing the hot isostatic pressing and heat treatment scheme, powder metallurgy hot isostatically pressed Ti2AlNb alloys can be obtained with uniform organization and balanced overall properties. It is found that: clean pre-alloyed Ti2AlNb powder can be prepared by the aerosolization process, and uniform chemical composition and organization can be obtained by the hot isostatic pressing process; the hot isostatic pressing temperature affects the bulk density and distribution of pores in powder metallurgy Ti2AlNb alloys. The results show that the hot isostatic pressing temperature affects the porosity distribution and mechanical properties of powder metallurgy Ti2AlNb alloys. After different post-heat treatments, the organization and mechanical properties of powder metallurgy Ti2AlNb alloy changed significantly, and a good combination of tensile strength, ductility and fracture life was obtained by optimizing the heat treatment process.
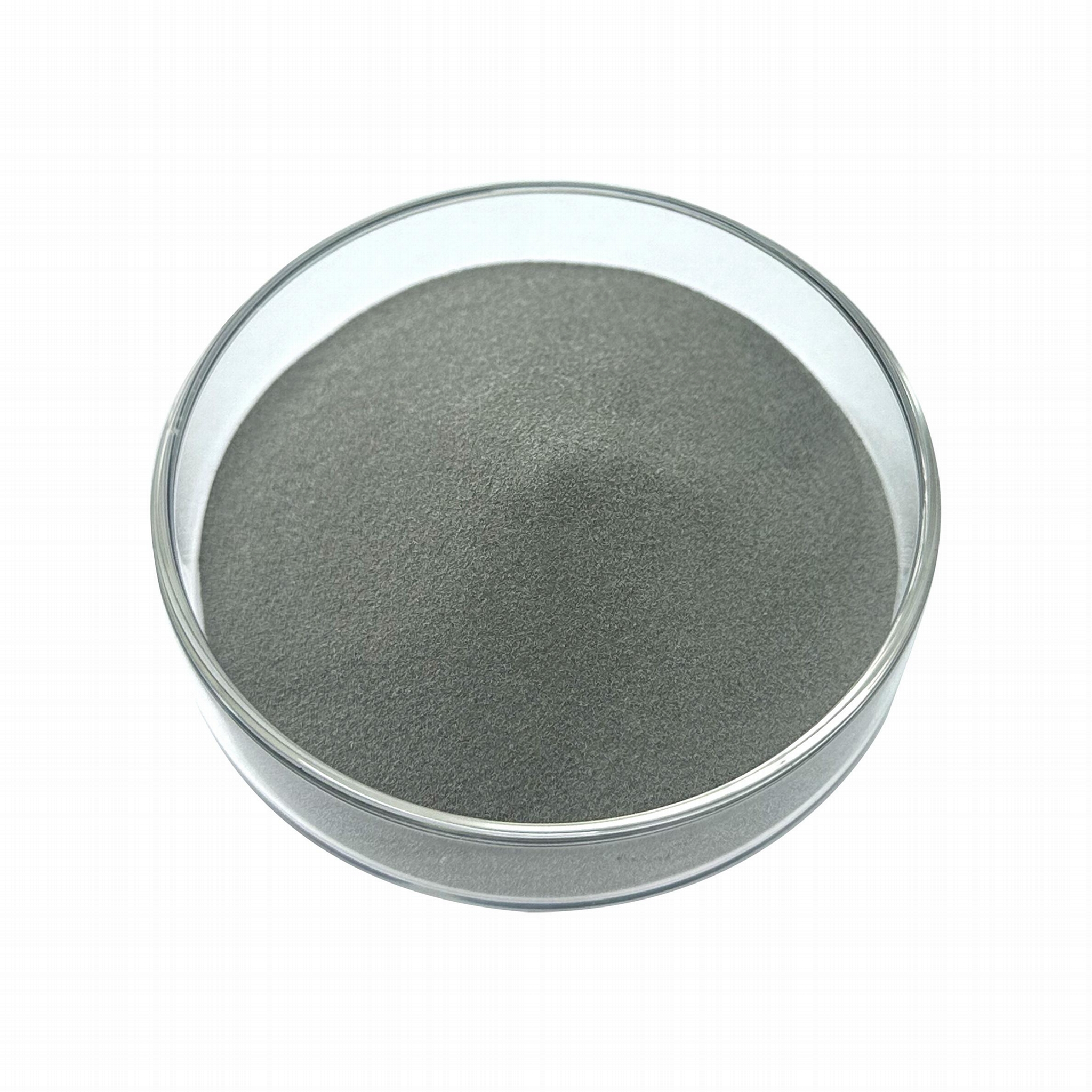